Poka-Yoke Solutions Robotics Alabama Engineering Companies Use to Eliminate Production Errors
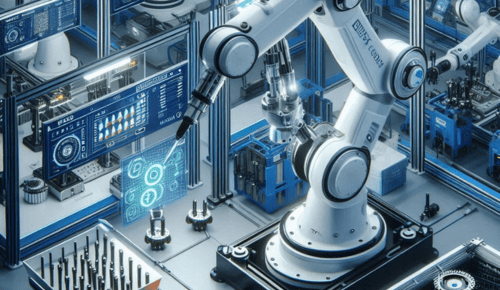
Mistakes in manufacturing can lead to wasted materials, higher costs, and lost productivity. That’s why robotics engineering companies in Alabama rely on poka-yoke, or error-proofing solutions, to ensure production lines run smoothly. By integrating smart robotics, manufacturers can eliminate defects before they become costly problems.
Error-Proof Robotic Pick-and-Place Techniques for Zero Defect Rates
Pick-and-place robotics play a vital role in modern manufacturing, reducing human error while speeding up production. These robots are programmed to handle components with precision, ensuring that each part is placed in its exact position without misalignment. By using vision systems and sensors, they verify the accuracy of each movement, preventing misplaced parts or skipped steps. In industries where even the smallest mistake can cause defects, these robots guarantee that every product meets quality standards before leaving the assembly line.
Alabama robotics engineering companies refine these systems further with intelligent adjustments based on real-time data. If an error is detected—such as a misaligned component—the robot corrects itself before continuing. This self-monitoring capability not only eliminates defects but also enhances efficiency. Pick-and-place robotics ensure that manufacturers maintain zero defect rates while increasing production speed, making them a core element in error-proofing strategies.
Robotic Verification Stations Immediately Identifying Assembly Faults
Verification stations powered by robotics provide an extra layer of quality control in manufacturing environments. These systems inspect assembled products in real time, identifying errors before they reach the next stage. Advanced cameras, sensors, and AI-driven algorithms scan for missing, misaligned, or incorrect components, catching defects early to prevent costly recalls or rework.
A robotics engineering company in Alabama may customize verification stations to fit specific production needs, from automotive parts to electronics assembly. When a fault is detected, the system either flags the product for correction or stops the production line to prevent further issues. This automated quality assurance process eliminates reliance on human inspectors, reducing the chances of oversight while ensuring consistent and accurate results across every unit produced.
Intuitive Robotics Halting Operations at the First Sign of Error
In traditional manufacturing, workers might miss subtle mistakes, allowing errors to pass through multiple stages before detection. Intuitive robotics prevent this by immediately stopping operations at the first sign of an issue. These robots constantly monitor performance metrics such as part dimensions, torque values, and alignment, pausing production if an anomaly is detected.
Alabama robotics engineering companies implement these intuitive systems to enhance both efficiency and safety. When an error occurs, the robot alerts operators, providing detailed diagnostics to pinpoint the problem. This instant feedback prevents defective products from progressing through the assembly line, saving manufacturers time and resources. By stopping problems before they escalate, intuitive robotics maintain high-quality output while reducing waste.
Tactile Feedback Automation Ensuring Components Snap into Perfect Position
Some manufacturing errors occur when parts are forced into place incorrectly, leading to misalignment, damage, or functional issues. Tactile feedback automation solves this problem by ensuring that each component is positioned with absolute precision. Robots equipped with force sensors detect the exact pressure needed for proper placement, preventing over-tightening or improper fits.
A robotics engineering company in Alabama might integrate these systems in industries requiring delicate assembly, such as aerospace or medical device manufacturing. When a part is being placed, the robot “feels” whether it has snapped into position correctly. If the fit isn’t perfect, it makes micro-adjustments until alignment is flawless. This level of precision guarantees that every component is securely installed, eliminating failures caused by improper assembly.
Smart Fixtures Eliminating Wrong-Part Installation Errors
One of the simplest yet most effective poka-yoke methods is the use of smart fixtures that physically prevent the installation of incorrect parts. These fixtures are custom-designed to fit only the right components, ensuring that workers or robots cannot mistakenly install the wrong piece.
Alabama robotics engineering companies often integrate these fixtures with automated systems, adding an extra layer of protection. If an operator attempts to install the incorrect part, the system locks it out, preventing the error from happening in the first place. This method is especially useful in high-precision industries where using the wrong component could lead to safety hazards or operational failures. By eliminating the possibility of mistakes at the source, smart fixtures maintain consistency in production while reducing costly rework.
Automated Torque Control Ensuring Perfect Assembly Tightness
Proper torque application is crucial in manufacturing, especially in industries where fasteners must be tightened to exact specifications. Automated torque control ensures that screws, bolts, and other fasteners are secured with the correct force, preventing issues like loose connections or stripped threads.
Robotics engineering companies in Alabama develop systems that measure and apply torque with unmatched precision. These automated tools not only tighten fasteners but also verify their integrity before moving to the next assembly stage. If a fastener is under- or over-tightened, the system flags it for correction. This poka-yoke method guarantees that every connection in an assembly is secure, reducing the risk of product failure while enhancing overall safety and reliability.